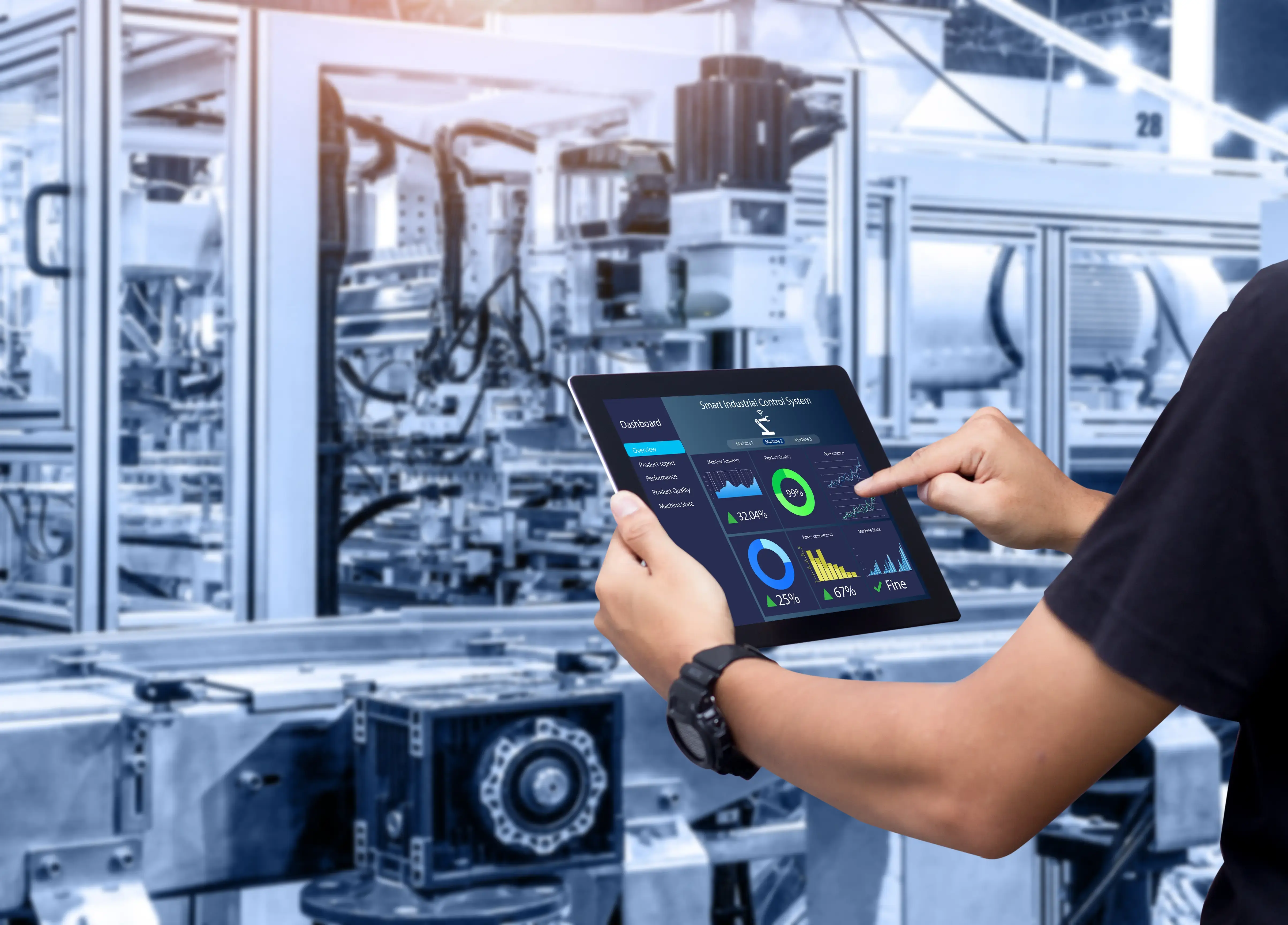
In today’s rapidly evolving manufacturing landscape, the ability to capture and act on data is key to staying competitive. Enter IO-Link, a communication protocol designed to make machines smarter and more connected. Whether you're running a large-scale operation or a small, agile factory, IO-Link has the potential to transform how you collect data, monitor performance, and maintain your equipment. Here are five reasons why IO-Link is the future of smart manufacturing.
Universal Compatibility
One of the standout features of IO-Link is that it's completely brand agnostic. That means it works with a wide range of sensors, actuators, and other devices, regardless of the manufacturer. Whether you're upgrading an existing system or designing a new one, IO-Link makes it easy to integrate smart devices without locking you into a single vendor. This level of flexibility simplifies maintenance, reduces equipment costs, and makes future expansions easier.
Simplified Installation and Configuration
In traditional systems, wiring and configuring each device can be time-consuming and prone to errors. IO-Link simplifies this process with standardized point-to-point communication, which allows you to connect smart devices using standard cables and connectors. Once connected, the system automatically recognizes and configures each device, reducing setup time and lowering the risk of installation errors. This also means fewer device replacements due to incorrect wiring or configuration.
Real-Time Data Collection
IO-Link enables the collection of real-time data directly from devices on the factory floor. Sensors equipped with IO-Link provide detailed information, such as temperature, pressure, vibration, and even diagnostics about their own health. With this level of data granularity, manufacturers can monitor machine performance, predict potential failures, and schedule maintenance proactively, reducing unplanned downtime and extending the life of their equipment.
Predictive maintenance is often seen as a luxury for larger manufacturers with complex SCADA or MES systems, but IO-Link brings this capability to manufacturers of all sizes. With its ability to gather detailed, real-time data from individual devices, IO-Link makes it easier to implement condition monitoring and predictive maintenance without needing to invest in expensive, large-scale software systems. For smaller manufacturers, this offers a cost-effective way to prevent machine breakdowns and increase operational efficiency.
Future-Proofing for Industry 4.0
As Industry 4.0 continues to drive digital transformation, having a smart, flexible communication protocol like IO-Link is essential for future-proofing your operations. IO-Link enables easy scalability, allowing you to add or replace devices as your operation grows, while its ability to integrate with existing Ethernet and cloud-based systems ensures your data is always accessible and actionable. With IO-Link, you're not just improving today’s production processes—you’re setting the foundation for tomorrow’s innovations.
Use Case: Streamlining Production with IO-Link for a Packaging Manufacturer
A mid-sized packaging manufacturer, specializing in flexible packaging solutions for the food and beverage industry, faced challenges in maintaining consistent quality and uptime on their high-speed filling and sealing lines. With a wide variety of products and frequent changeovers, they needed a more efficient way to monitor and control multiple smart devices across their production lines without excessive downtime or complicated setups.
The manufacturer implemented IO-Link technology to standardize communication across various sensors and actuators on their equipment, including pressure sensors, proximity sensors, and valve actuators. By connecting these devices to IO-Link masters, they were able to create a fully decentralized IO architecture, reducing wiring complexity and enabling rapid device configuration during product changeovers.
One significant improvement was on their filling line, where IO-Link pressure sensors monitored the consistency of liquid fill levels with extreme precision. When variations in pressure were detected, the system immediately adjusted valve actuators to maintain accurate fill rates, ensuring product consistency without interrupting the production flow. Previously, this kind of adjustment required manual recalibration, resulting in downtime.
Additionally, IO-Link’s real-time data collection allowed the maintenance team to monitor the health of sensors and actuators. During routine production, an IO-Link-enabled proximity sensor showed signs of degrading performance, which triggered an alert in the system. Maintenance was able to replace the sensor during a scheduled downtime window, preventing an unexpected failure.
By adopting IO-Link, the manufacturer saw a 25% reduction in product changeover times due to faster sensor reconfiguration, a 15% improvement in overall equipment effectiveness (OEE), and a 10% reduction in maintenance-related downtime. The standardized IO-Link network also reduced wiring costs and simplified troubleshooting, leading to increased operational efficiency.
Why IO-Link Matters
Whether you're looking to improve data collection, simplify device integration, or implement cost-effective predictive maintenance, IO-Link provides the flexibility and scalability you need to stay competitive. Its universal compatibility and real-time data capabilities make it a perfect fit for manufacturers who want to unlock the full potential of their machines and transition into the era of smart manufacturing. Contact your local NEFF representative to learn more about IO-Link.
About the author - Dave Roth is a Product Manager at Neff Automation with a passion for helping manufacturers embrace Industry 4.0 technologies. With years of experience in industrial automation and a deep understanding of condition monitoring and data-driven solutions, Dave is dedicated to empowering businesses to improve efficiency and reduce downtime through smart, scalable innovations.