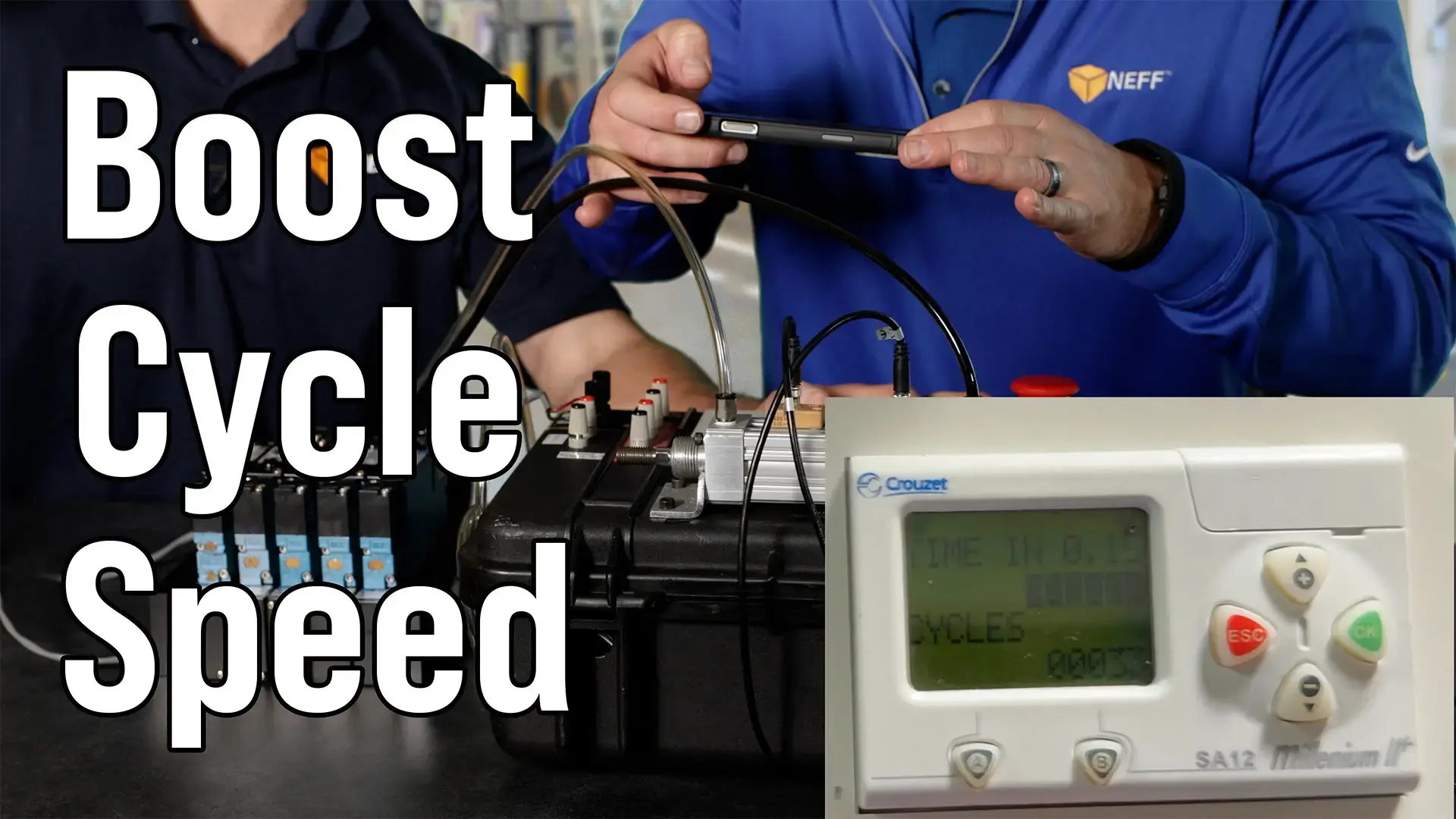
When it comes to pneumatic systems, even small adjustments can lead to significant improvements in speed and efficiency. This blog explains how optimizing pneumatic systems can result in faster cycle speeds—a crucial factor for boosting productivity in industrial automation. Here, we’ll break down the key takeaways from their demo and provide actionable insights to help you enhance your pneumatic performance.
The Problem: Slow Cycle Speeds
One of the most common questions asked by operators is how to improve the speed of pneumatic cylinders. In many setups, the valve stack is positioned several feet away from the cylinder for accessibility. While convenient, this arrangement often results in slower cycle speeds due to the length of tubing required to connect the components. Operators frequently attempt to address this by increasing air pressure, but as Doug Grogg explains, this approach is not always effective.
The Key to Speed: Flow, Not Just Pressure
Air pressure primarily impacts force, while flow dictates speed. Increasing pressure might help overcome initial friction, but it doesn’t address the underlying issue: the inefficiency caused by long tubing runs. By focusing on optimizing air flow, operators can achieve faster cycle speeds without overloading the system.
The Experiment: Short Tubing vs. Long Tubing
To highlight the impact of tubing length, the NEFF team conducted a series of tests using a Mac Valves 92 Series valve (1.2 CV) paired with a PHD CV cylinder. They compared cycle speeds using two different tubing lengths (2 feet and 10 feet) and varied air pressures (40 PSI and 80 PSI). Here are the results:
-
10 Feet of Tubing at 40 PSI: The system achieved 45 cycles in 15 seconds.
-
2 Feet of Tubing at 40 PSI: The shorter tubing resulted in 83 cycles in the same timeframe—nearly double the speed.
-
10 Feet of Tubing at 80 PSI: Increasing the pressure improved the cycles to 59 in 15 seconds, but this was still far less efficient than the shorter tubing.
-
2 Feet of Tubing at 80 PSI: With shorter tubing, the system achieved an impressive 93 cycles in 15 seconds.
The Solution: Move Valves Closer to the Action
The tests clearly demonstrate that minimizing tubing length significantly improves cycle speed. By relocating valves closer to the actuator, operators can reduce air travel time and optimize flow. This simple change can almost double the efficiency of your pneumatic system, as shown in the 93-cycle result compared to 45 cycles with longer tubing.
For manufacturers, faster cycle speeds translate to higher throughput and reduced downtime. Whether you’re working with packaging machines, material handling systems, or other automated equipment, optimizing your pneumatic setup can provide a competitive edge.
If you’re looking to enhance your system’s performance, Neff Automation can help. From selecting high performance valves and cylinders to designing optimized layouts, our team has the expertise to boost your efficiency. Check out the full demonstration in the video below for more details and contact your NEFF representative to get started.
Watch the full demo here: