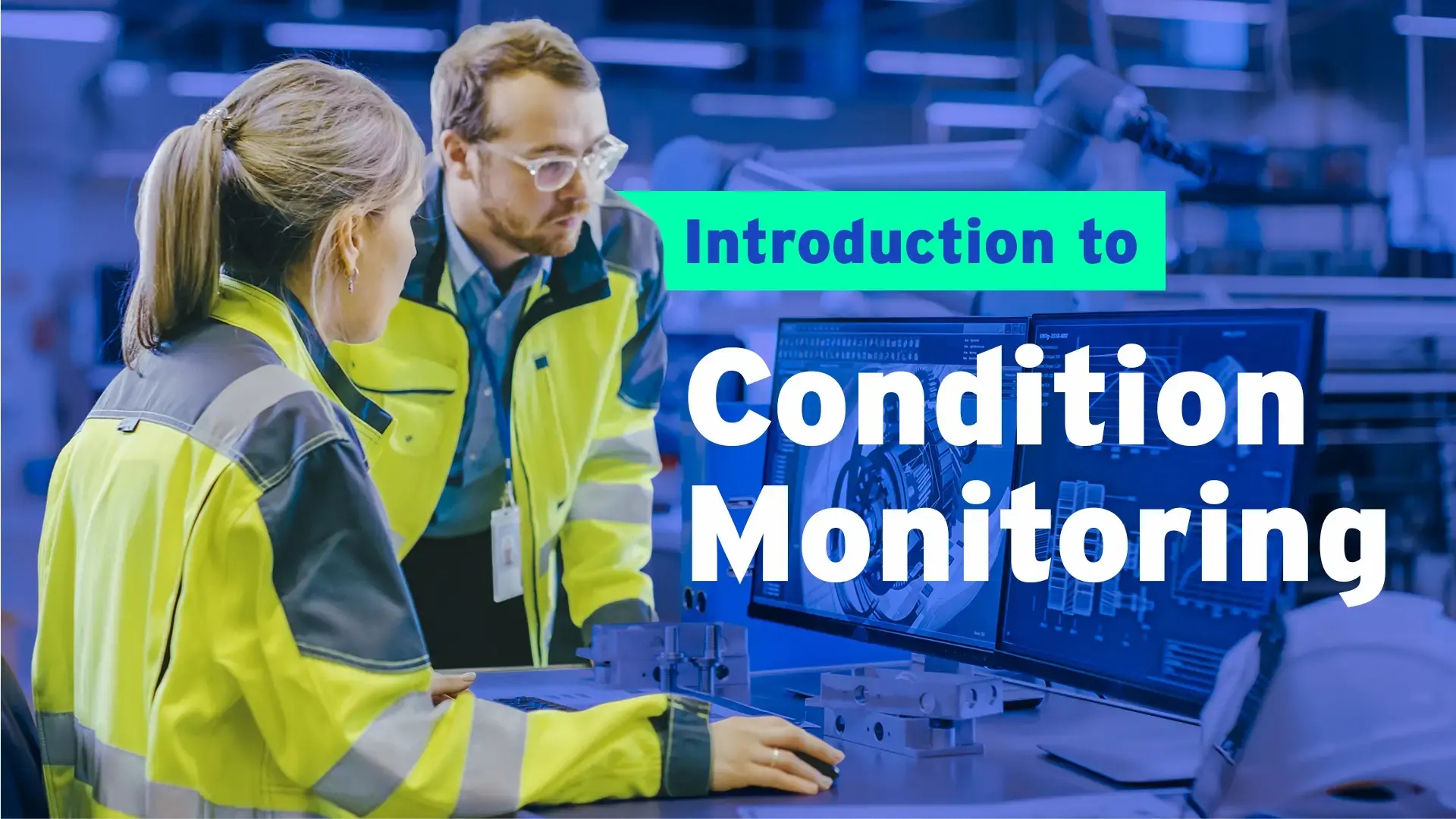
Unplanned downtime is one of the biggest threats to efficiency in manufacturing. When machines stop unexpectedly, it can disrupt production, increase costs, and delay deliveries—creating a ripple effect throughout your operations. But what if there was a way to stay ahead of potential failures before they happen? That’s where condition monitoring comes into play.
Condition monitoring involves the continuous tracking of machine health through the use of smart sensors that provide real-time data on the performance and wear of critical components. By implementing condition monitoring, manufacturers can detect small issues before they turn into costly breakdowns. Here’s how it works—and how it can save your factory from unplanned downtime.
Detect Early Signs of Wear and Tear
The key to avoiding downtime is knowing when a machine is starting to fail. Condition monitoring systems use sensors to track factors like vibration, temperature, pressure, and more. These sensors capture even the smallest deviations from normal operating conditions, providing early warning signs of wear and tear. This allows maintenance teams to address potential issues before they lead to a full-blown machine failure.
Move from Reactive to Proactive Maintenance
Without condition monitoring, many manufacturers rely on reactive maintenance—fixing machines only after they break. This approach can be costly and disruptive. By shifting to a proactive maintenance strategy with condition monitoring, you can schedule maintenance at the right time, reducing the need for emergency repairs and minimizing the impact on production.
Increase Equipment Lifespan
Machines that are maintained based on real-time performance data tend to last longer. Condition monitoring helps you maintain equipment more efficiently, ensuring that parts are replaced when they need to be, not too early or too late. This optimized maintenance schedule reduces unnecessary wear and keeps machines running at peak performance for longer periods.
Improve Safety on the Production Floor
When machines fail, there’s not only the risk of lost production but also the possibility of safety hazards. Condition monitoring can help identify critical issues before they pose a risk to workers. By catching problems early, you can prevent unsafe working conditions and ensure compliance with safety standards.
Use Case: Preventing Downtime with Balluff's Condition Monitoring Toolkit
A mid-sized automotive parts manufacturer recently adopted Balluff’s Condition Monitoring Toolkit (CMTK) to monitor critical assets on their stamping line. Using Balluff’s BCM sensors on key motors and press components in their stamping line, they tracked critical metrics like vibration amplitude, bearing temperature, and runtime hours. One motor in particular, responsible for powering the main hydraulic press, had exhibited intermittent vibration spikes—something that would have gone unnoticed without continuous monitoring.
By analyzing the real-time data collected from the CMTK dashboard, the maintenance team detected early signs of bearing fatigue in the motor. Instead of waiting for a failure, they scheduled the repair during a planned maintenance window over the weekend. This proactive move avoided what could have been a catastrophic motor failure during peak production the following week, which would have caused significant delays in delivering parts to their automotive OEM customer. The result? A 18% reduction in unplanned downtime, a 7% improvement in overall equipment effectiveness (OEE), and extended asset life. The integration with their PLC network also allowed for automated alerts, ensuring the team stays ahead of future equipment issues.
Optimize Production Efficiency
By avoiding unplanned downtime and keeping machines running smoothly, condition monitoring leads to better overall efficiency. Your production schedules become more reliable, and your team can focus on maximizing output rather than troubleshooting breakdowns. This kind of operational stability leads to higher throughput and, ultimately, improved profitability.
A Smarter Approach to Maintenance
Condition monitoring is no longer just for large manufacturers with complex systems. Thanks to affordable, scalable technologies, even small and mid-sized factories can implement condition monitoring solutions to reduce unplanned downtime, extend the lifespan of their equipment, and improve safety. With the right sensors in place, you can gain visibility into your operations and prevent small issues from becoming costly problems.
Watch the video here:
About the author - Dave Roth is a Product Manager at Neff Automation with a passion for helping manufacturers embrace Industry 4.0 technologies. With years of experience in industrial automation and a deep understanding of condition monitoring and data-driven solutions, Dave is dedicated to empowering businesses to improve efficiency and reduce downtime through smart, scalable innovations.