How MAC Pulse Valves Improved Energy Efficiency at a Smelter
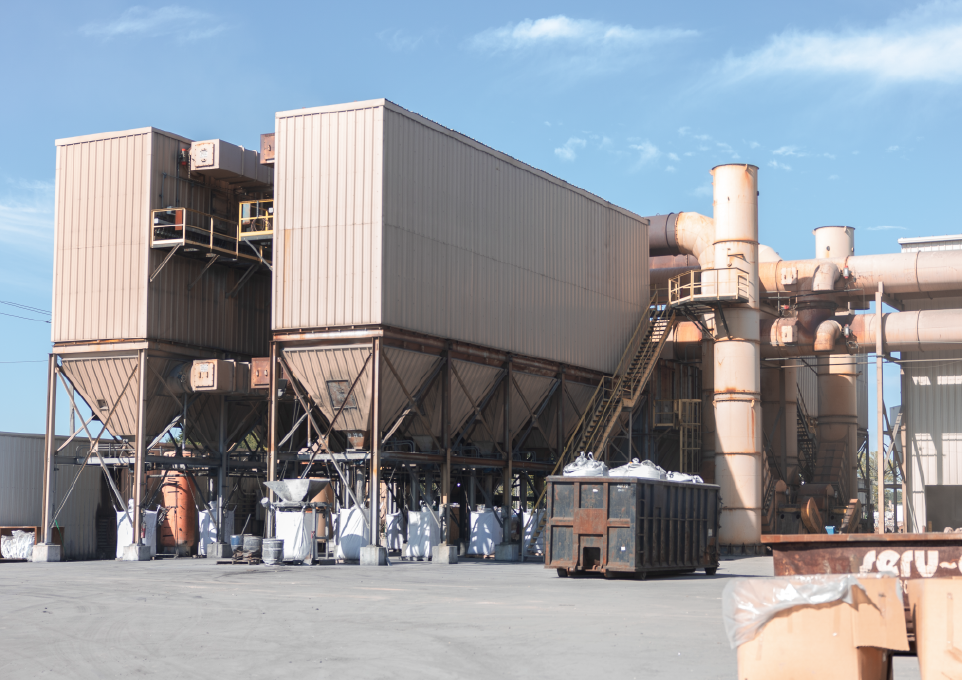
Industry
Metals
Challenge
The customer was facing issues with their baghouse. High energy costs and frequent valve changes drove them to look for better options.
Results
After testing 95 MAC Pulse Valves and seeing instant results, the Aluminum Smelter decided to go ahead with over 300 total valves, completely eliminating their previous diaphragm valves. This results in nearly $65K of annual energy, filter life, and maintenance savings.
"We're not having the same problems, less repairs are needed, and we knew this would help reduce compressed air."
Maintenance Manager
Leading Aluminum Smelting Company
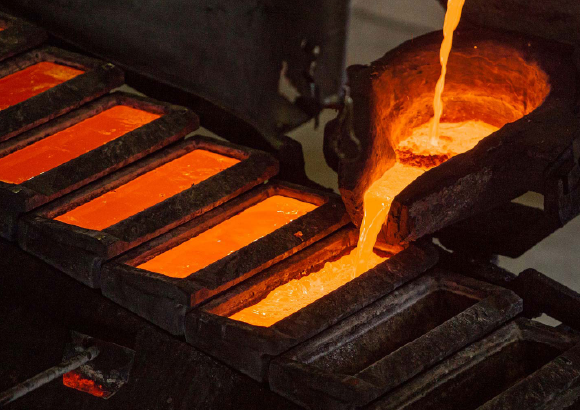
Aluminum Smelting
Aluminum smelting is a critical step in creating pure aluminum alloy for use in the transportation, construction, and packaging industries. Dust, gas, and other byproducts are generated that effect air quality, which is tightly monitored for workplace safety. Traditional filtration and dust collection systems are utilized to improve air quality, but these systems are often equipped with outdated valve technology that can lead to poor sustainability and high energy usage.The Challenge
NEFF Automation recently worked with a leading aluminum smelting company that was facing two major problems with their dust collection system:
- High Maintenance Costs: Daily maintenance demands were straining resources and causing operational inefficiencies.
- Excessive Air Consumption: Leaking valves, which the company wasn’t even aware of, were driving up air consumption, leading to significant energy waste and added costs.
It’s easy to see how these issues were a constant headache. Maintenance problems slow down production, and leaking valves are essentially money slipping away. NEFF identified the baghouse as an area of focus for process improvement and energy savings. The benefits of switching to MAC Pulse Valves include increased cleaning capacity per pulse, reduced compressed air demand, extended bag life, and much more.
The Solution
Once the customer's problems were clearly identified, NEFF brought in a demo case so the aluminum smelting company could see how MAC's Pulse Valve technology worked. This demonstration made the customer confident that switching from their old diaphragm valves to MAC Pulse Valves would promote sustainability and energy efficiency.
"I haven't seen one negative thing on the valves that we have installed." Maintenance Manager @ Leading Aluminum Smelter Company
The Results
Initially, the customer was going to test 95 valves for one bag house. Because of the customer's confidence in NEFF's products, evaluation process, and a strong projected ROI, the customer decided to skip the trial process and go with a full-plant conversion!
NEFF Automation supports metal manufacturers across the Midwest and Northeast by implementing cost-effective, sustainable solutions that promote energy efficiency and operational cost reduction.
Watch the case study video below: